Uusioaines Ltd is a pioneer of the circular economy, processing at its Forssa plant some 70 per cent of all recyclable glass collected in Finland. It fully re-uses its raw material. After processing the glass goes into industrial use or, depending on quality, Uusioaines makes foam glass from it. Foam glass is an ecofriendly insulating product and lightweight fill.
The landscape in Uusioaines Ltd’s yard looks like another planet. Snow covers huge mounds and conical heaps. One contains returnable bottles, another a year’s harvest of laminated glass. The Extra I class of plate glass radiates a turquoise light. This is the company’s store of raw materials.
“We collect and recycle packaging glass and plate glass, from which we manufacture cullet, glass powder and foamed glass. The largest supplier of packaging glass is Palpa, a company managing the systems for returning beverage packages. Plate glass comes from glass-handling, glass-cutting and glass-processing businesses,” explains Managing Director Jussi Parkkali.
Uusioaines is Finland’s first and only cleaning and processing plant for recyclable glass. Some 80,000 tonnes a year of collected glass pass through the plant, representing about 70 per cent of all recyclable glass collected in Finland. The plant’s capacity would be sufficient to clean all the recyclable glass collectable in Finland.
“Every year, we export from Finland tens of thousands of tonnes of recyclable glass for processing abroad. We also buy glass from abroad as raw material for our foam glass ” explains Parkkali.
Uusioaines is a pioneer in glass cleaning and processing
We put on safety shoes, safety vests, helmets, goggles, hearing protectors and respiratory protectors. We climb up a steel-grid stairway to the top level of the glass-cleaning plant. A layer of very fine dust covers the railings, and the machinery makes the floor vibrate. Somewhere over there, our household jars and wine bottles are ground into pieces that Uusioaines sells to Saint-Gobain Isover’s plants in Forssa and Hyvinkää for transforming into glass wool insulation, or that are exported as raw material for new bottles and jars.
“There’s not a single glass furnace left in Finland that can utilise recyclable glass, if you don’t count the manufacture of glass wool. The nearest manufacturing furnaces for glass packaging are in Estonia, Sweden and Russia,” says Development Manager Jari Pennanen.
The family company, which later became Uusioaines Ltd, was originally in the gravel business. In the 1980’s, some glass was also crushed in stone crushers. When Leevi Stenberg, founder of the Stenberg companies, retired in 1987, mechanical engineering technician Jari Stenberg took over the helm. He became familiar with glass as a material at the nearby Ahlström Isover (nowadays Saint-Gobain) glass wool factories.
Some 70 per cent of glass wool insulation is made from recyclable glass. Finland has been a pioneer in this field, partly due to testing jointly conducted by Ahlström and Uusioaines.
“The circular economy typically functions in chains, in which companies supplement each other by using each other’s wastes or surpluses. All the links of the chain are important to their common purpose. This can also be seen here in the Forssa region, where companies in the circular economy employ a lot of people,” Parkkali points out.
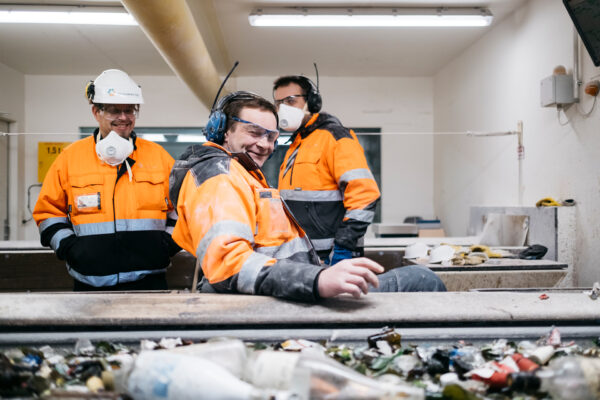
Cleaning recyclable glass a manual and machine vision job
Lemminkainen acquired the Stenberg companies’ other parts in 1997, leaving the glass-crushing operations. In 1991, when state alcohol monopoly Alko started charging a deposit charged on all returnable bottles, Uusioaines received under contract all bottles that could not be washed and refilled. This ensured a steady supply of glass and allowed investment: the first glass processing plant was commissioned in 1994, and a new, more efficient plant in 2010.
“Detecting metal lids, capsules and other impurities with a camera and their automated separation have been tried since 1993. I was involved when the glass-cleaning plant was designed and built, and when industrial-scale glass-cleaning was started in early 1995. Nevertheless, the initial sorting of recyclable glass is still a manual process,” says Pennanen as he opens the door to the sorting room situated at the very top of the processing plant.
In initial sorting, rubbish bags, porcelain scraps and other larger impurities are picked off the conveyor belt, after which the glass continues its journey in the plant’s process. Aluminium, metal and can tops drop little by little into their own piles outside the plant. From there they are transported onwards to Eurajoki for later use. Glass falls into its own piles, cleaned and sorted by colour.
Construction of the glass-cleaning plant cost almost EUR 10 million. Currently, it operates for about 40 hours a week, because there is no more glass supply.
“Doing good deeds is not a privilege of charitable organisations; companies can also promote sustainable values. Because an activity is profitable doesn’t mean that it’s bad. The development work Uusioaines did is unique and we’ve every reason to be proud of it,” says Parkkali, who became Managing Director of Uusioaines in 2017.
Full re-use of glass through foam glass production
The site accommodates another plant. In its yard are piles of foam glass aggregate, which looks like lumps of stone. The lumps are surprisingly light to hold in the hand, though.
“Many people like to believe that glass recycling is an endless loop, in which used glass is melted and re-used over and over again. This is not, however, completely accurate. About 20 per cent of the glass to be fed into the cleaning process breaks down during collection, transportation and processing and becomes so fine that full cleaning and colour sorting of it is not viable. Uusioaines uses this fine material to manufacture Foamit foam glass aggregate, an earthworks product competing with expanded clay aggregate,” explains Parkkali.
“The manufacture of foam glass and the glass grades for industry supplement each other. We manage to recycle one hundred per cent of the glass we receive,” adds Pennanen.
The foam glass plant completed in 2010 is now on a service stand-down. Usually the plant’s furnaces glow with heat and the ball mills produce deafening noise as they grind the glass material. Now all is quiet. The men are making a precision adjustment, replacing a wing in the air classifier that sorts powdered glass by size.
Glass fragments are ground into a fine powder, 0.1 mm in grain size, and a foaming agent is added. When heated in the furnace, the glass mass expands to fivefold its size and hardens into foam glass. Foam glass is full of small air bubbles and on cooling it becomes hardened glass foam. At the output end of the process, the foam glass starts to split into smaller chunks due to the thermal stresses, forming crushed foam glass.
“Foamit foam glass aggregate is lightweight, non-combustible, frost-resistant and thermally insulating. It has better bearing strength than competing materials, and its high friction coefficient makes it easy to handle. In infrastructure construction, foam glass is ideal as frost-heave insulation as well as a bulk lightening material. In house-building, it is suitable as a filler for floors and roofs and also cellar wall footings,” lists Pennanen.
The manufacture of foam glass is not a Finnish invention; it has been manufactured in Switzerland since the 1980s. Most foam glass from Nordic countries is used in Norway.
Impetus for growth and internationalisation
Last autumn Uusioaines received new owners when the Oulu-based investment company Partnera acquired a 58 per cent holding. Tesi also became an owner of the company by buying a 30 per cent share. With the new owners’ support, Uusioaines intends to continue as a pioneer of the circular economy, as well as to grow and internationalise. Parkkali reports there are a number of growth and development plans in progress. The company will use Foamit as a springboard for internationalisation.
“One opportunity is to duplicate our operating model in a European country lacking foam glass manufacturing capacity. We’ve looked at the Netherlands, whose exceptionally strict environmental requirements Foamit already meets. Another option is to expand through acquisitions,” Parkkali explains.
In Finland, Uusioaines envisages growth opportunities with glass sand, as well as with Foamit, because sandblasting with glass sand is safer than with quartz sand. Glass sandblasting is a milder technique than blasting with metal shot or quartz sand, but is more effective than sodablasting.
“We’re also planning our own energy production. There’s nothing to prevent us from gasifying the waste plastics we collect into fuel with which to heat our furnaces,” Pennanen muses.
“Neither is developing new products ruled out, because our value added could be higher,” adds Parkkali.
Photos: Junnu Lusa
Uusioaines Ltd
What it does: Cleans and processes recyclable glass. Also manufactures and sells foam glass, an ecofriendly insulating product and lightweight fill. Receives about 70 per cent of all Finland’s recyclable glass. Exports some 34,000 tonnes of glass a year for the manufacture of recycled glass products. Saint-Gobain produces glass wool from 30,000 tonnes of this. Uusioaines produces foam glass from about 16,000 tonnes of the remainder, but it also imports raw material for foam glass.
Where it is: Office in Jokioinen and plants in Forssa, Finland.
Net sales: EUR 15 million
Personnel: 33.
Owners: Investment company Partnera Oy, Tesi, Jarkir Oy and Jussi Parkkali.
Websites: https://www.uusioaines.com/, https://www.foamit.fi/